Have you ever thought about how much time and effort goes into ensuring vehicles are properly inspected? While some shops still rely on old-school, paper-based methods for auto repair inspections, others have jumped into the digital age.Â
But here’s the question: Is doing an auto repair inspection without software still the best way to go?
The old-school way: What’s the process?
Before software solutions took over, auto repair shops had to rely on manual inspections. Mechanics would inspect vehicles, jot down findings on paper forms, and communicate issues verbally to the service advisor before passing it onto the customer. Simple, right? Well, in theory, yes.
Here’s a quick peek at the typical steps involved in a paper-based inspection:
Â
- Inspection by hand: The mechanic physically inspects the car, often referring to checklists or notes to make sure everything is checked.
Â
- Paperwork: All findings, from brake conditions to engine issues, are written down manually on paper forms.
Â
- Manual record-keeping: At the end of the day, all records are filed away in physical storage—making it tough to access them later for reference.
Sounds like a lot of room for error, doesn’t it? But before software tools, this was the norm. Let’s take a look at how these manual processes stack up in today’s fast-paced world.
The problem with old-school inspections
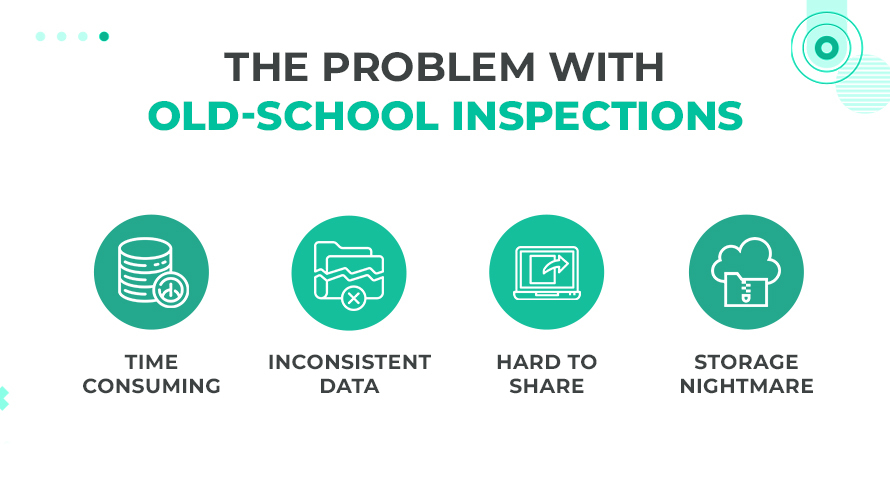
Sure, relying on paper for inspections may seem like a cost-effective solution at first, but let’s dive deeper into the challenges it presents:
- Time-consuming: Have you ever watched a mechanic flip through pages, trying to find an old inspection report? With paper-based systems, information isn’t easily accessible, which can waste a lot of time.
- Inconsistent data: Writing things down manually means human error is a real possibility. A mechanic might accidentally miss a crucial part of the inspection or the front desk may misread their handwriting, causing issues later on.
- Hard to share: Imagine a mechanic finishing a report at the end of a long day, only to realize that they can’t share the findings with a colleague who needs it immediately.
- Storage nightmares: Paper documents need to be stored and organized—if they’re not, things can get lost, making it tough to keep track of past inspections.
These challenges might not seem like a big deal on the surface, but they can add up to real problems in your workflow.
Why software makes a difference in auto repair inspections
So, how do modern auto repair shops streamline their inspections and avoid the headaches of paperwork? Enter inspection software. By moving away from paper and adopting digital tools, repair shops can experience a world of difference.
Here’s how software can make inspections smoother:
Â
- Faster inspections: Digital tools make it easier to record inspection results quickly and accurately. No more writing things down or flipping through endless pages.
Â
- Error-free data: With automated prompts and checklists, the software helps ensure that no vital parts of the vehicle are missed during the inspection.
Â
- Instant access: No more digging through stacks of paper—everything is stored securely and can be accessed at the click of a button.
Â
- Better communication: Reports can be shared instantly with customers or other staff members, reducing delays and miscommunication.
Â
- Data-driven insights: Inspection software can automatically analyze patterns in your data, identifying recurring issues and helping mechanics stay ahead of potential problems.
How DVI transforms inspections:
- Streamlined Inspections: Mechanics can use tablets or mobile devices to complete inspections with digital checklists.
- Visual Proof: DVI allows you to add photos and videos of vehicle issues, which can be shared directly with customers.
- Faster Approvals: Clear visuals help customers understand the problems, leading to quicker approvals for repairs.
- Better Records: All inspections are stored digitally, making them easy to retrieve and reference in the future.
Real-life example: Ace Auto Clinic
Take the example of Ace Auto Clinic, a shop located in the heart of the city that has been serving its community for over two decades. Like many shops, Ace Auto Clinic initially relied on paper-based systems. However, they faced constant challenges:
Â
- Disorganized paperwork that caused delays.
- Slow processes that frustrated customers.
- Difficulty tracking jobs and inventory.
To solve these problems, Ace Auto Clinic implemented AutoLeap, complete with its DVI feature. The results were transformational:
Â
- Faster processes: Inspections were completed quicker with digital tools, saving hours every week.
- Improved transparency: Customers received detailed inspection reports with visuals, building trust and leading to faster repair approvals.
- Streamlined operations: Job tracking and inventory management became seamless.
Here’s what Sal, the shop’s owner, had to say:
“As a shop owner, AutoLeap has tremendously helped us grow our profits, project the future, and do a better job at streamlining our business.”
But, is software the right choice for everyone?
While software can offer a lot of advantages, it’s not always the right choice for every shop. Some shops may have limited budgets or may not be ready to make the transition to digital tools. If you’re in this boat, here are a few things to consider before making the leap:
- Budget: Software tools do come with upfront costs, though many offer affordable pricing for small businesses.
- Training: Switching to new software means your team may need training to use it effectively. This can be time-consuming but is usually well worth the effort in the long run.
- Customer preferences: Some customers might prefer the more personal touch of a handwritten report. It’s important to gauge customer feedback before making any changes.
Should you go digital?
It’s clear that doing an auto repair inspection without software is becoming increasingly outdated. While there are still shops that rely on paper forms, the benefits of using digital tools—like speed, accuracy, and ease of access—are hard to ignore. The world is moving forward, and so should your shop!
By making the switch to software, you can offer faster, more reliable inspections that keep customers happy and your workflow smooth. And who knows? You might just find that ditching the paper is the best move you’ve ever made.
Now, next time someone asks about the best way to handle auto repair inspections, you can confidently say, “Go digital!” Trust me, your future self (and your customers) will thank you.